Introduction to Tablet Press Feeding Systems
Tablet presses are sophisticated machines at the heart of pharmaceutical manufacturing, transforming powder mixtures into precisely formed tablets. While compression mechanisms often receive the most attention, the feeding system is equally critical—it's responsible for delivering the correct amount of material to the die cavity before compression occurs. The feeding method you select impacts production efficiency, tablet uniformity, and overall product quality.
Various feeding systems have evolved to address different formulation characteristics and production requirements. From the simplicity of gravity-fed systems to advanced forced feeders with multiple paddles, each solution offers distinct advantages and limitations that pharmaceutical manufacturers must consider.
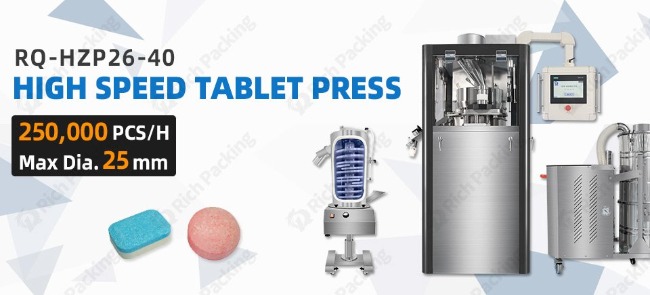
Why Feeding Methods Matter in Tablet Compression
The feeding system's performance directly influences several critical aspects of tablet production:
Weight Uniformity
Consistent die filling ensures tablets maintain uniform weight, which directly correlates with proper medication dosing. Even minor variations in die filling can lead to significant dosage inconsistencies, particularly for low-dose active ingredients.
Production Speed
Advanced feeding systems can maintain proper die filling at higher speeds, enabling manufacturers to maximize throughput without compromising quality.
Material Handling Capabilities
Different powder characteristics (flowability, density, cohesiveness) require specific feeding approaches to prevent issues like bridging, segregation, or incomplete die filling.
Equipment Longevity
Proper feeding reduces mechanical stress on tablet press components, extending the operational life of expensive tooling and reducing maintenance requirements.
Types of Tablet Press Feeding Methods
1. Gravity Feeding System
The gravity feeding system represents the simplest approach to tablet press feeding, relying on gravity to move powder from the hopper into the die cavities.
How Gravity Feeding Works
In this system, powder flows naturally from the hopper through a feed frame positioned directly above the die table. As the turret rotates, empty dies pass beneath the feed frame, allowing gravity to fill them with powder. The excess powder is scraped away by a leveling mechanism before compression.
Advantages of Gravity Feeding
- Simplicity: Minimal moving parts mean fewer maintenance requirements
- Gentle Handling: Reduced mechanical stress on delicate formulations
- Cost-Effectiveness: Lower initial investment compared to more complex systems
- Less Heat Generation: Minimal friction prevents temperature-sensitive materials from degradation
Limitations of Gravity Feeding
- Flow-Dependent Performance: Requires excellent powder flowability
- Speed Limitations: Struggles to maintain consistent filling at higher production speeds
- Density Variation Sensitivity: Prone to weight variations with materials that have inconsistent bulk density
- Feed Frame Design Constraints: Limited optimization options for challenging formulations
Suitable Applications
Gravity feeding systems work best with:
- Free-flowing, non-sticky powders
- Formulations with excellent flowability characteristics
- Lower-speed production requirements
- Products where simplicity and minimal powder manipulation are priorities
2. Force Feeder Systems
Force feeding systems employ mechanical means to actively move powder into die cavities, overcoming limitations associated with gravity-dependent methods.
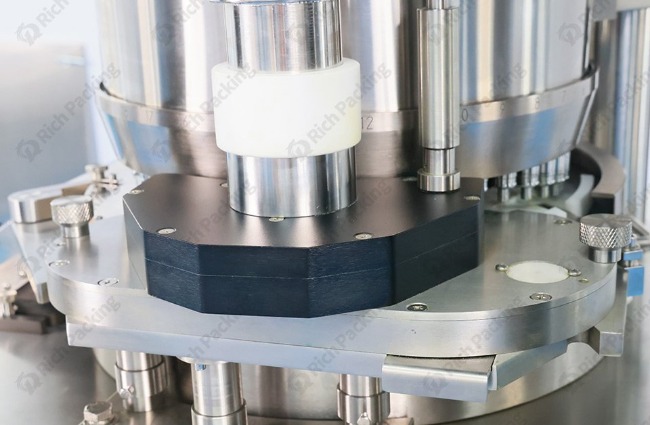
How Force Feeding Works
Force feeders utilize rotating paddles or wheels within the feed frame to:
- Drive powder horizontally toward and into the die cavities
- Break up potential powder bridges or clumps
- Create consistent powder density within the feed frame
- Ensure complete die filling regardless of natural flow properties
Single Paddle Force Feeders
The most basic force feeder configuration uses a single paddle wheel rotating within the feed frame. This design:
- Provides basic powder movement to enhance flow
- Creates some level of densification through paddle action
- Offers improved consistency compared to gravity feeding
- Maintains relatively simple maintenance requirements
Multiple Paddle Force Feeders
Advanced force feeders implement two or more paddle wheels, typically with:
- A larger, slower-rotating outer paddle for initial powder movement
- A smaller, faster-rotating inner paddle for final die filling
- Independent speed controls for process optimization
- Specially designed paddle configurations for specific formulation types
Advantages of Force Feeding
- Flow Independence: Successfully processes powders with poor flow characteristics
- Higher Production Speeds: Maintains consistent filling at increased turret speeds
- Process Control: Adjustable paddle speeds allow optimization for different formulations
- Enhanced Uniformity: Produces more consistent tablet weights across production runs
- Densification Control: Ability to modify the degree of powder compaction in the feed frame
Limitations of Force Feeding
- Mechanical Complexity: More moving parts increase maintenance requirements
- Potential Overworking: Excessive paddle action may alter powder properties
- Heat Generation: Friction from paddles can increase powder temperature
- Higher Cost: More sophisticated systems require greater initial investment
- Potential for Segregation: Paddle action may cause particle separation in some formulations
Suitable Applications
Force feeders excel with:
- Powders with poor flow characteristics
- High-speed production requirements
- Formulations requiring consistent densification
- Manufacturing scenarios where weight precision is critical
3. Vacuum Feeding Systems
Vacuum feeding represents a specialized approach for challenging materials, utilizing negative pressure to assist powder movement into die cavities.
How Vacuum Feeding Works
In vacuum-assisted feeding:
- A vacuum is applied beneath the die table at the filling position
- Negative pressure draws powder from the feed frame into the die cavity
- The vacuum is released after filling but before compression
- Often combined with force feeding for optimal results
Advantages of Vacuum Feeding
- Superior Performance with Difficult Materials: Effectively handles extremely poor-flowing powders
- Reduced Segregation: Minimizes particle separation during the filling process
- Enhanced Die Filling: Ensures complete filling of deep or complex die geometries
- Consistent Results with Low-Density Materials: Particularly effective with fluffy or low-density formulations
- Weight Consistency: Achieves weight uniformity even with challenging powders
Limitations of Vacuum Feeding
- System Complexity: Requires additional components and controls
- Maintenance Requirements: Vacuum systems need regular cleaning and inspection
- Filter Management: Requires careful attention to filter maintenance
- Higher Cost: Represents a significant investment compared to other feeding systems
- Process Validation Challenges: Adds another variable requiring careful control
Suitable Applications
Vacuum feeding systems are ideal for:
- Extremely cohesive or poor-flowing powders
- Low-density, fluffy materials
- Deep or complex die configurations
- High-value products where maximum weight precision justifies the investment
- Formulations prone to segregation issues
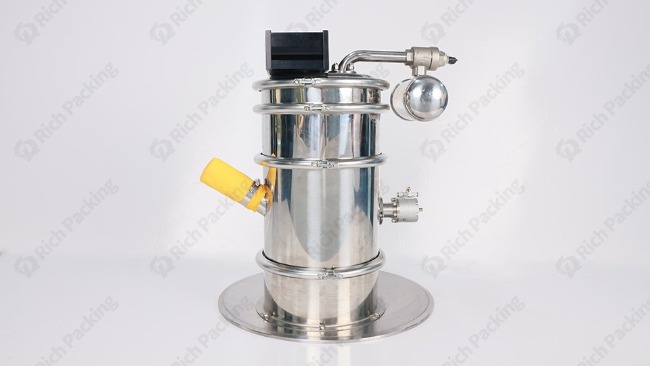
Selecting the Optimal Feeding Method
Formulation Considerations
Material Characteristic |
Recommended Feeding Method |
Excellent flowability |
Gravity feeding |
Moderate flowability |
Single paddle force feeder |
Poor flowability |
Multiple paddle force feeder |
Very poor flowability |
Force feeding with vacuum assistance |
Low density/fluffy |
Vacuum or specialized force feeder |
Prone to segregation |
Carefully controlled force feeding |
Sensitive to mechanical stress |
Gravity or gentle single paddle |
High-speed production |
Advanced force feeding systems |
Production Requirement Factors
When selecting a feeding system, consider these production elements:
- Production Volume: Higher volumes typically justify more sophisticated feeding systems
- Required Precision: Critical medications may demand advanced systems for weight consistency
- Changeover Frequency: Simpler systems offer faster cleaning and changeover
- Available Operators: Complex systems require skilled personnel for proper operation
- Budget Constraints: Balance immediate cost against long-term efficiency benefits
- Product Portfolio: Diverse product range may require more versatile feeding capabilities
Optimizing Your Tablet Press Feeding System
Feed Frame Design Considerations
Modern feed frames incorporate sophisticated design elements:
- Overhanging Feed Frame: Prevents powder from falling outside the die table
- Integrated Powder Level Sensors: Maintain optimal powder depth in the feed frame
- Polished Surfaces: Reduce friction and prevent powder adhesion
- Specialized Coatings: Non-stick surfaces for challenging formulations
- Temperature Control: Cooling systems for heat-sensitive materials
- Observation Windows: Allow visual monitoring of powder flow
- Cleanable Design: Quick-disconnect features for efficient sanitization
Process Parameter Optimization
Fine-tuning these parameters can dramatically improve feeding performance:
- Paddle Speed Ratio: Adjusting the relationship between outer and inner paddles
- Feed Frame Powder Level: Maintaining optimal depth for consistent filling
- Turret Speed Relationship: Synchronizing feeding with turret rotation
- Vacuum Strength: Finding the optimal negative pressure for assistance
- Vibration Settings: Determining appropriate frequency and amplitude
- Dosing Disc Selection: Choosing appropriate thickness and opening size
- Pre-Compression Settings: Affecting powder redistribution in the die
Monitoring and Control Systems
Advanced tablet presses incorporate:
- Real-time Weight Monitoring: Continuous feedback on tablet weight
- Automated Paddle Speed Adjustment: Dynamic changes based on weight trends
- Powder Level Control: Automated hopper systems maintaining optimal fill
- Force-vs-Time Analytics: Identifying filling inconsistencies through compression profiles
- Integration with Process Analytical Technology: Continuous quality verification
- Data Logging Capabilities: Historical performance tracking for continuous improvement
Common Feeding-Related Challenges and Solutions
Weight Variation Issues
Problem |
Possible Causes |
Recommended Solutions |
Systematic weight variation |
Inconsistent die filling |
Adjust feed parameters; consider more advanced feeding system |
Random weight spikes |
Feed frame bridging |
Optimize paddle configuration; consider vibration assistance |
Progressive weight drift |
Powder property changes |
Implement real-time monitoring with feedback control |
Cyclical weight pattern |
Mechanical synchronization issues |
Evaluate timing between feeding and turret systems |
Initial weight inconsistency |
Inadequate feed frame priming |
Establish proper startup procedures |
Flow Problems
Common flow challenges include:
- Bridging: Powder forms arches that prevent consistent flow
- Rat-holing: Vertical channels form in the powder mass
- Flushing: Sudden powder surges during operation
- Sticking: Powder adheres to feed frame surfaces
- Segregation: Separation of blend components during feeding
Solutions typically involve:
- Adjusting feed system parameters
- Modifying formulation characteristics
- Implementing alternative feeding technologies
- Applying specialized coatings to contact surfaces
- Reconsidering blend preparation techniques
Future Trends in Tablet Press Feeding Technology
Smart Feeding Systems
Next-generation feeding technology incorporates:
- Artificial Intelligence: Adaptive systems that learn optimal parameters
- Predictive Analytics: Anticipating feeding issues before they affect production
- Self-Optimization: Systems that continuously adjust for optimal performance
- Digital Twin Technology: Virtual modeling of feeding behavior
- Integration with Industry 4.0: Connected feeding systems sharing data across the manufacturing environment
Material-Specific Innovations
Emerging technologies address specific feeding challenges:
- Electrostatic Control: Neutralizing charges that affect powder behavior
- Ultrasonic Assistance: High-frequency vibration for challenging materials
- Microwave Technology: Modifying powder surface characteristics
- Novel Paddle Designs: Engineered for specific powder types
- Advanced Surface Treatments: New coatings with superior non-stick properties
Continuous Manufacturing Integration
As pharmaceutical manufacturing evolves toward continuous processing:
- Direct Blend-to-Press Feeding: Eliminating intermediate storage steps
- Real-time Formulation Adjustment: Adapting to input material variations
- Continuous Feedback Loops: Maintaining critical quality attributes
- Multi-Dimensional Process Control: Simultaneous optimization of multiple parameters
- Regulatory Compliance Features: Built-in data collection for continuous verification
Conclusion
The feeding method you choose for your tablet press significantly impacts production efficiency, tablet quality, and manufacturing consistency. By understanding the different feeding technologies available—from simple gravity systems to sophisticated force feeders with vacuum assistance—you can select the optimal approach for your specific formulation and production requirements.
For personalized guidance on selecting the right tablet press feeding system for your unique manufacturing needs, contact our pharmaceutical equipment specialists today. Your product's success begins with proper powder feeding.