Introduction
Are you struggling to properly implement blister packaging for your products? Mastering blister packaging techniques can significantly enhance your product protection, presentation, and consumer experience. This comprehensive guide will walk you through everything you need to know.
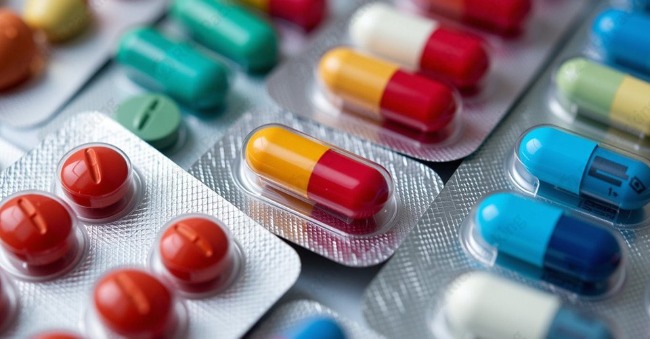
Understanding Blister Packaging Fundamentals
What Is Blister Packaging?
Blister packaging consists of a pre-formed plastic cavity or pocket, usually transparent, with a backing of paperboard, aluminum, or plastic film. This versatile packaging solution has become increasingly popular across industries for its numerous advantages.
The structure typically includes:
- A thermoformed plastic bubble (the "blister")
- A backing card or foil seal
- Optional additional barrier layers
- Tamper-evident features
Types of Blister Packaging
Understanding the different types of blister packaging will help you select the most appropriate option for your specific needs:
1. Clamshell Packaging
Clamshell blister packages feature two thermoformed pieces hinged together, resembling a clamshell. This design offers excellent product visibility while providing robust protection. You'll commonly find this type used for:
- Electronics and accessories
- Toys and small gadgets
- Hardware items
- Medical devices requiring sterile environments
2. Face-Seal Blister Packaging
Face-seal blisters attach a pre-formed plastic bubble to a backing card using heat and pressure. This cost-effective option works well for lightweight products requiring visual display. You'll often see face-seal blisters used for:
- Retail consumer goods
- Stationery items
- Small household products
- Light pharmaceutical products
3. Full-Face Blister Packaging
Full-face blisters extend the plastic component to cover the entire front surface of the backing card. This design offers enhanced product protection and premium presentation. Consider this style for:
- High-value retail goods
- Products requiring maximum visibility
- Items with detailed display requirements
- Premium brand positioning
4. Trapped Blister Packaging
Trapped blister designs sandwich the product between two cards with a window cutout. This approach offers excellent printing space while still allowing product visibility. Ideal applications include:
- Cosmetics and personal care items
- Premium retail products
- Items requiring extensive product information
- Products benefiting from upscale presentation
Key Materials Used in Blister Packaging
The effectiveness of your blister packaging largely depends on the materials you select:
Plastic Materials:
Material |
Benefits |
Best For |
PVC (Polyvinyl Chloride) |
Cost-effective, clear, easily thermoformed |
Non-sensitive consumer goods |
PET (Polyethylene Terephthalate) |
Recyclable, excellent clarity, good barrier properties |
Environmentally-conscious applications |
PETG (Polyethylene Terephthalate Glycol) |
Enhanced durability, better thermal resistance |
Products requiring extra protection |
PP (Polypropylene) |
Chemical resistance, higher temperature tolerance |
Pharmaceutical applications |
COC (Cyclic Olefin Copolymer) |
Superior moisture barrier, high clarity |
Moisture-sensitive products |
Backing Materials:
- Paperboard: Economical, printable, environmentally friendly
- Aluminum foil: Excellent barrier properties, tamper-evident
- Plastic film: Transparent backing option for full product visibility
- Composite materials: Combining multiple layers for enhanced protection
Benefits of Blister Packaging
Implementing proper blister packaging techniques offers numerous advantages for both manufacturers and consumers:
Product Protection
Blister packaging excels at protecting products from:
- Environmental factors (moisture, dust, oxygen)
- Physical damage during transportation and handling
- Tampering and contamination
- UV radiation and light exposure
Enhanced Product Display
You'll benefit from improved visual merchandising through:
- Clear product visibility for consumer inspection
- Customizable backing cards for branding and information
- Hanging options for efficient retail display
- Space-efficient design for maximum shelf impact
Extended Shelf Life
For pharmaceutical and food products, blister packaging significantly extends shelf life by:
- Creating barrier protection against moisture and oxygen
- Maintaining sterility for medical products
- Preventing cross-contamination between individual units
- Protecting against degradation factors
Consumer Convenience
Your customers will appreciate the user-friendly aspects:
- Unit-dose packaging for pharmaceuticals
- Easy identification of product contents
- Portion control for consumables
- Child-resistant options when required
Step-by-Step Guide to Using Blister Packaging
Step 1: Evaluate Your Product Requirements
Before implementing blister packaging, you must carefully assess your product's specific needs:
Product Dimensions and Weight
Measure your product accurately, accounting for:
- Length, width, and height dimensions
- Weight distribution
- Any protrusions or irregular shapes
- Quantity per package unit
Protection Requirements
Identify the specific protection your product requires:
- Moisture sensitivity level
- Oxygen barrier needs
- Light protection requirements
- Impact resistance necessary
- Temperature stability range
Display and Marketing Considerations
Determine how your product should be presented:
- Visibility requirements
- Branding space needed
- Regulatory information that must be included
- Retail display environment
Step 2: Select the Appropriate Blister Packaging Type
Based on your evaluation, choose the most suitable blister packaging configuration:
For Pharmaceuticals:
Pharmaceutical products typically require:
- Push-through foil-backed blisters for tablets and capsules
- Child-resistant designs where mandated
- Unit-dose packaging for precise medication management
- High barrier protection against moisture and oxygen
For Consumer Electronics:
Electronics benefit from:
- Anti-static blister materials
- Clamshell designs for premium protection
- Custom-molded cavities to secure components
- Tamper-evident features to prevent retail theft
For Retail Consumer Goods:
General retail products often use:
- Face-seal blisters for economical packaging
- Custom-shaped cavities that highlight product features
- Hanging holes for pegboard display
- Enhanced graphics on backing cards
For Food Products:
Food items require:
- Food-grade approved materials
- Modified atmosphere packaging options
- Easy-open features for consumer convenience
- Portion control capabilities
Step 3: Design Your Blister Package
Creating an effective blister package design involves:
Cavity Design
Develop precise cavity specifications:
- Allow 1-2mm clearance around the product
- Consider draft angles for easy product insertion
- Design cavity depth appropriate for product height
- Account for stacking requirements in shipping
Backing Card Design
Create effective backing cards with:
- Clear branding elements
- Required regulatory information
- Scannable barcodes and QR codes
- Consumer instructions when needed
Seal Area Planning
Plan proper seal areas:
- Minimum 5-8mm seal width for adequate strength
- Even seal area distribution around the cavity
- Reinforced seal areas for heavier products
- Appropriate texture for optimal adhesion
Step 4: Select Materials Based on Requirements
Choose materials strategically based on product needs:
Barrier Requirements
For sensitive products requiring protection:
- High MVTR (Moisture Vapor Transmission Rate) barriers for humidity protection
- Oxygen barrier properties for oxidation-sensitive items
- UV protection for light-sensitive products
- Temperature-stable materials for items experiencing temperature fluctuations
Sustainability Considerations
For environmentally conscious packaging:
- PET or recycled PET for recyclable plastic components
- FSC-certified paperboard for backing cards
- Biodegradable options where appropriate
- Minimized material usage through optimal design
Cost Optimization
Balance protection with economics:
- Material thickness appropriate to protection needs
- Efficient cavity designs to minimize waste
- Standard sizes to reduce tooling costs
- Multi-cavity designs for production efficiency
Step 5: Implement the Manufacturing Process
The production process involves several critical stages:
Thermoforming
For the blister component:
- Heat the selected plastic sheet to pliable temperature
- Form it over a mold using vacuum or pressure
- Allow cooling while maintaining shape
- Trim excess material for precise dimensions
Filling Operations
Insert products with care:
- Ensure clean environment for product placement
- Position products precisely within cavities
- Verify proper placement before sealing
- Implement quality checks throughout the process
Sealing Process
Create secure seals with:
- Heat sealing for most applications
- RF (Radio Frequency) sealing for specific materials
- Ultrasonic sealing for specialty applications
- Cold sealing for temperature-sensitive products
Finishing Operations
Complete the packaging with:
- Die-cutting to final dimensions
- Perforation for multi-unit packages
- Adding hanging holes when needed
- Final inspection for quality assurance
Step 6: Implement Quality Control Measures
Ensure packaging integrity through comprehensive quality checks:
Visual Inspection
Verify aesthetic and structural quality:
- Uniform cavity formation
- Proper product placement
- Clear visibility of contents
- Printing quality and alignment
Seal Integrity Testing
Confirm seal effectiveness with:
- Bubble leak tests
- Vacuum decay testing
- Pressure differential testing
- Dye penetration for critical applications
Material Testing
Validate material properties through:
- Thickness measurements
- Barrier property verification
- Impact resistance testing
- Accelerated aging tests
Functional Testing
Ensure user experience quality:
- Opening force requirements
- Child-resistance verification where applicable
- Drop testing for transit protection
- Environmental condition simulations
Step 7: Optimize Storage and Transportation
Protect your blister-packaged products during distribution:
Storage Conditions
Maintain optimal environment:
- Temperature control within specified range
- Humidity management for moisture-sensitive packages
- Protection from direct sunlight and UV exposure
- Proper stacking to prevent crushing
Transportation Considerations
Ensure safe transit:
- Secondary packaging to protect blister integrity
- Efficient case packing for distribution
- Orientation guidelines to prevent damage
- Clear handling instructions for shippers
Advanced Blister Packaging Techniques
Sustainable Blister Packaging Innovations
Embrace eco-friendly approaches:
Material Reduction Strategies
- Thin-walling techniques for reduced plastic usage
- Right-sizing cavities to minimize material
- Elimination of unnecessary packaging components
- Structural design optimization
Recyclable Solutions
- Mono-material designs for easier recycling
- PET blisters with PET backing for single-stream recycling
- Easily separable components
- Recycling instruction inclusion on packaging
Biodegradable Alternatives
- PLA (Polylactic Acid) blister materials
- Cellulose-based films for certain applications
- Plant-based backing card alternatives
- Compostable adhesives and inks
Smart Blister Packaging Technology
Incorporate advanced functionality:
Track-and-Trace Features
- RFID-enabled blister packs
- QR codes linked to product information
- Serialization for authenticity verification
- Supply chain tracking integration
Compliance Monitoring
- Electronic adherence monitoring for pharmaceuticals
- Time-stamped opening detection
- Patient compliance reporting
- Integration with healthcare management systems
Interactive Elements
- NFC-enabled packaging for consumer engagement
- Augmented reality features through smartphone scanning
- Temperature indicators for cold chain monitoring
- Authentication features for brand protection
Common Blister Packaging Challenges and Solutions
Sealing Issues
Problem: Inconsistent seals leading to package failure
Solutions:
- Standardize sealing parameters (temperature, pressure, dwell time)
- Implement regular maintenance of sealing equipment
- Use seal strength testing in quality control
- Consider alternative sealing materials for problematic products
Material Selection Errors
Problem: Inappropriate material selection causing product degradation
Solutions:
- Conduct material compatibility testing with product
- Implement accelerated stability studies
- Consult with material suppliers for specialized applications
- Consider multi-layer barriers for highly sensitive products
Production Efficiency Challenges
Problem: Slow production speeds or high rejection rates
Solutions:
- Optimize tooling design for efficient thermoforming
- Implement vision systems for automated quality inspection
- Design packages with manufacturing efficiency in mind
- Balance automation with quality requirements
Environmental Concerns
Problem: Consumer and regulatory pressure for sustainable packaging
Solutions:
- Develop recycling partnerships for collection and processing
- Educate consumers on proper disposal methods
- Invest in innovative sustainable materials
- Design for circularity from the beginning
Industry-Specific Blister Packaging Applications
Pharmaceutical Blister Packaging
The pharmaceutical industry relies heavily on blister packaging for:
- Unit-dose medication presentation
- Patient compliance enhancement
- Counterfeit protection
- Stability improvement for sensitive medications
Best Practices:
- Implement child-resistant designs where required
- Use high-barrier materials for moisture-sensitive drugs
- Include clear dosing instructions on backing
- Follow all regulatory requirements for pharmaceutical packaging
Consumer Electronics Blister Packaging
Electronics manufacturers benefit from blister packaging through:
- Theft deterrence features
- Product visibility at point of sale
- Protection from static and physical damage
- Brand enhancement through premium presentation
Best Practices:
- Use anti-static materials for sensitive components
- Design custom-fit cavities for precise component protection
- Incorporate easy-open features for consumer convenience
- Balance security with accessibility
Food Industry Applications
Food producers utilize blister packaging for:
- Portion control servings
- Freshness preservation
- Tamper evidence
- Attractive merchandising
Best Practices:
- Select food-grade approved materials
- Consider gas flushing for extended shelf life
- Design for consumer convenience in opening
- Balance protection with sustainability concerns
Conclusion
Mastering blister packaging techniques requires attention to detail, material knowledge, and process optimization. By following this comprehensive guide, you've gained the essential knowledge to implement effective blister packaging solutions for your products. Have questions about implementing blister packaging for your specific application? Contact us today for expert consultation.