Introduction
You are about to explore a comprehensive guide on how to adjust the tablet weight during the operation of the tablet press. This article will equip you with the knowledge and practical steps to fine-tune both your Tablet Press machine and Rotary Tablet Press machine. As an experienced industry expert, I will walk you through the technical, operational, and maintenance aspects vital for ensuring consistent tablet weight and overall product quality.
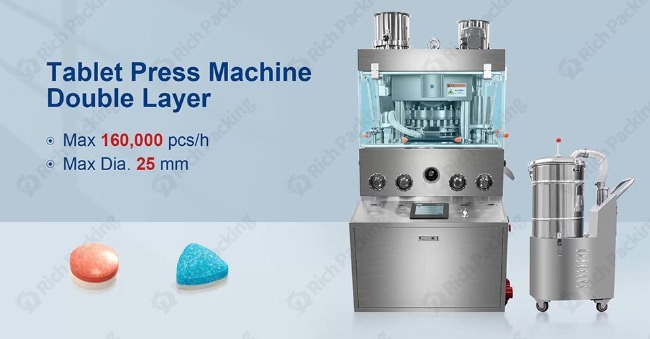
Understanding Tablet Press Machines
You must first understand the machinery at the heart of your production line. Tablet press machines come in various designs and capabilities, each engineered to convert raw materials into the finished tablet product with precision.
What Is a Tablet Press Machine?
A Tablet Press machine is used to compress powder or granules into tablets of uniform shape, weight, and hardness. Its operation involves several critical elements:
- Powder Feeding: Raw materials are supplied to the machine in a controlled manner.
- Compression Process: The machine uses high-pressure components to compress materials into tablets.
- Ejection System: Tablets are ejected from the machine, ready for further quality checks or packaging.
Types of Tablet Press Machines
There are two primary types of tablet press machines that you will encounter:
Understanding these machines is crucial because adjusting tablet weight depends on the specific operation and technology inherent in each machine type.
The Importance of Tablet Weight Consistency
You must realize that maintaining consistent tablet weight is not just a quality parameter—it is a regulatory requirement. Inaccuracies in tablet weight can lead to dosage variations that may compromise the efficacy, safety, and market acceptability of your products.
Quality and Regulatory Implications
- Patient Safety: Variations in tablet weight may lead to improper dosage, affecting treatment outcomes.
- Regulatory Compliance: Regulatory bodies such as the FDA require strict adherence to dosage uniformity standards.
- Brand Integrity: Consistent tablet weight reinforces consumer trust and supports your brand’s reputation.
Each tablet that leaves your production line must conform to rigorous quality control tests, making your adjustments critically important.
Factors Influencing Tablet Weight
You need to consider multiple factors that affect tablet weight during production. These factors can be broadly divided into machine-related elements, material properties, and process parameters.
1. Machine Factors
The physical and technical aspects of your tablet press machine play a crucial role:
- Die and Punch Alignment: Misalignment can cause uneven compression and variable tablet weight.
- Compression Force: The amount of pressure applied during compression directly influences tablet density and weight.
- Machine Calibration: Regular calibration ensures that the machine produces tablets within the specified weight range.
2. Material Characteristics
The properties of the raw materials also affect tablet weight:
- Powder Granularity: The particle size distribution and cohesiveness determine how well the material compresses.
- Moisture Content: Variations in moisture can alter the flow and compressibility of the blend.
- Lubricants and Binders: These additives influence the mechanical properties of tablets and must be controlled meticulously.
3. Process Parameters
Several operational parameters are adjustable to ensure proper tablet weight:
- Feed Rate: A consistent flow of material into the machine is crucial for uniform filling.
- Compression Cycle Time: The timing of the compression cycle affects the tablet formation process.
- Environmental Conditions: Ambient temperature and humidity levels can impact material behavior and machine performance.
Preparing for Weight Adjustment
You need to perform several preliminary checks and setup procedures to adjust the tablet weight effectively. Preparation ensures that your machine is ready for fine-tuning.
Pre-Operational Checks
Before initiating any adjustments, complete the following steps:
- Inspect the Machine: Verify that all components of the Tablet Press machine or Rotary Tablet Press machine are in good condition.
- Review Calibration Records: Check the latest calibration data to identify any deviations from target weight specifications.
- Examine Material Quality: Confirm that the raw materials meet the required standards for granularity, moisture, and composition.
- Set Environmental Controls: Ensure that production conditions such as temperature and humidity are within optimal ranges.
Documenting Baseline Parameters
Creating a baseline of your current operating conditions is essential:
- Record Tablet Weight: Document the weight and other critical quality attributes of a few sample tablets.
- Gather Process Data: Note down the current settings for feed rate, compression force, and cycle time.
- Identify Variances: Use statistical process control to identify any notable variability in tablet weight.
Having this data at hand will guide your adjustments and serve as a reference for measuring improvement.
Step-by-Step Guide to Adjusting Tablet Weight
You can now move into the heart of this guide—step-by-step adjustments to fine-tune tablet weight during operation. This process involves modifying both machine settings and process parameters.
Step 1: Adjusting Compression Force
The compression force is a critical determinant of tablet weight:
- Identify the Optimal Force: Based on your baseline data, determine if the compression force is too high or too low.
- Modify Machine Settings: Use the machine’s control panel to adjust the force settings.
- Test and Observe: After adjustments, run a short production batch and measure the tablet weight.
- Fine-Tune: Incrementally adjust the force until the target tablet weight is consistently achieved.
Step 2: Modifying the Feed Rate
Feed rate adjustments directly influence the amount of powder that enters the die:
- Observe Tablet Uniformity: Inconsistencies in feed rate can lead to weight variations.
- Calibrate the Feed System: Adjust settings to ensure a uniform and consistent feed rate.
- Use Sensors: Some machines offer real-time monitoring to track feed rate changes.
- Test the Output: Run a test batch and measure the tablet weight to assess any improvements.
Step 3: Fine-Tuning Compression Cycle Time
Cycle time adjustments can influence how material settles in the die:
- Review Cycle Time Settings: Shorter or longer cycles may affect tablet density.
- Trial Adjustments: Modify the cycle time in small increments and monitor the resulting tablet weight.
- Monitor Consistency: Ensure that changes in cycle time do not adversely impact other quality parameters like hardness.
- Reassess Performance: Utilize process control charts to verify that adjustments result in improved consistency.
Step 4: Calibrating the Die and Punch Alignment
Misalignment can result in uneven tablet formation:
- Inspect Alignment: Periodically check the alignment of the die and punches using precision instruments.
- Adjust Components: Make necessary mechanical adjustments to realign the components properly.
- Run Test Presses: Conduct trial runs to ensure that the alignment corrections produce tablets with consistent weight.
- Record Calibration Data: Document the alignment settings for future reference.
Step 5: Modifying Material Properties
Material handling plays a significant role in tablet weight:
- Control Moisture Levels: Use dehumidifiers or humidifiers as needed to maintain optimal moisture content.
- Optimize Powder Blending: Ensure that the material blend is homogeneous before compression.
- Review Lubricant Levels: Adjust the concentration of binders and lubricants to achieve desired compressibility.
- Perform Sample Testing: Analyze small batches to confirm that the material properties contribute positively to weight consistency.
Advanced Techniques for Tablet Weight Adjustment
Beyond the basic adjustments, advanced techniques can help fine-tune the process further.
Step 6: Utilizing Digital Control Systems
Digital control systems provide real-time insights and automated adjustments:
- Implement Digital Monitoring: Integrate digital sensors to continuously track feed rate, force, and cycle time.
- Use Feedback Loops: Automated control systems can adjust parameters dynamically based on sensor data.
- Monitor Performance Trends: Employ software analytics to identify patterns in tablet weight deviations.
- Optimize Settings Automatically: Some advanced Tablet Press machines allow for auto-calibration based on the collected data.
Step 7: Integration of IoT and Cloud-Based Analytics
Connecting your tablet press machine to an IoT network can further optimize performance:
- Real-Time Data Collection: Use IoT sensors to collect data from every aspect of the machine.
- Cloud-Based Analysis: Utilize cloud services to process and analyze the data, offering insights for further adjustments.
- Predictive Adjustments: Leverage predictive analytics to identify issues before they impact tablet weight.
- Automated Alerts: Set up alerts for deviations from established parameters to prompt immediate action.
Step 8: Operator Training and Continuous Improvement
No technique can replace the value of a well-trained operator:
- Regular Training Sessions: Ensure that your operators are familiar with both manual and digital adjustment techniques.
- Simulation Drills: Conduct simulation sessions to practice troubleshooting and adjustment procedures.
- Knowledge Sharing: Encourage operators to share insights and successful techniques within the team.
- Standardize Procedures: Maintain updated SOPs and training manuals based on evolving best practices.
Troubleshooting Common Issues During Adjustment
Despite best efforts, you might encounter challenges when adjusting tablet weight. The following troubleshooting tips can help you identify and correct issues quickly.
Issue 1: Inconsistent Tablet Weight Despite Adjustments
Issue 2: Poor Tablet Hardness Post-Adjustment
Issue 3: Frequent Machine Jams During Operation
Issue 4: Digital Feedback Inconsistencies
Preventive Maintenance for Consistent Tablet Weight
You must adopt preventive maintenance practices to minimize future adjustments and equipment downtime.
Regular Maintenance Schedules
Implement the following maintenance routine for your Tablet Press machine:
-
Daily Tasks:
- Visual inspections for obvious wear and contamination.
- Check power supplies and digital interface function.
-
Weekly Tasks:
- Clean the feeder, die, and punch components.
- Verify sensor alignment and recalibrate if necessary.
-
Monthly Tasks:
- Perform comprehensive machine calibration.
- Assess material handling processes and adjust environmental controls.
-
Quarterly Tasks:
- Schedule professional servicing and software updates.
Creating Standard Operating Procedures (SOPs)
Developing well-documented SOPs is essential:
- Detail Each Process: Include adjustments for feed rate, compression force, and cycle time.
- Operator Guidelines: Provide troubleshooting steps, preventive checks, and maintenance protocols.
- Regular Updates: Revise SOPs as new techniques and equipment improvements become available.
Following these maintenance schedules and SOPs ensures smooth operation and minimal deviation in tablet weight.
Comparative Analysis: Tablet Press Machine vs. Rotary Tablet Press Machine
You need to understand the differences in adjustment techniques between conventional and rotary models. Below is a detailed table comparing key aspects:
Parameter |
Tablet Press Machine |
Rotary Tablet Press Machine |
Operation Mode |
Semi-automated or fully manual adjustments possible |
Fully automated with continuous operation; advanced digital controls |
Feed System |
Typically relies on manually monitored feed rates |
Uses high-speed feeders with digital consistency controls |
Compression Force |
Adjustable via manual settings; periodic recalibration needed |
Automatically regulated with sensor-based feedback |
Cycle Time |
Fixed cycles with occasional manual adjustments |
Variable cycles managed by computer algorithms |
Maintenance Frequency |
More frequent manual checks required |
Integrated diagnostics reduce frequency of manual intervention |
Adjustment Complexity |
Simpler controls; easier for basic troubleshooting |
Advanced features requiring detailed digital calibration |
This table helps you decide which machine best suits your production capacity and adjustment precision requirements.
Case Studies and Real-World Examples
Learning from real-world examples can provide practical insights into tablet weight adjustment. Consider the following case studies:
Case Study 1: Adjusting Tablet Weight in a Small-Scale Production Facility
A boutique pharmaceutical manufacturer uses a Tablet Press machine to produce customized dosage forms. They encountered variations in tablet weight due to inconsistent feed rates. By:
- Implementing Daily Checks: Increased operator vigilance.
- Adjusting the Compression Force: Fine-tuned the settings using small incremental changes.
- Recalibrating Sensors: Regular calibration improved weight consistency. Result: Tablet weight variability decreased by 30%, leading to enhanced product quality.
Case Study 2: High-Speed Production with a Rotary Tablet Press Machine
A large-scale manufacturer using a Rotary Tablet Press machine noted a gradual drift in tablet weight across high-speed batches. They addressed the issue by:
- Integrating IoT Sensors: For real-time monitoring of feed rate and compression force.
- Updating Firmware: To utilize advanced auto-calibration features.
- Implementing Predictive Maintenance: Based on data analytics. Result: Production consistency improved significantly, with a 25% reduction in weight deviation and fewer production stoppages.
Advanced Strategies for Tablet Weight Adjustment
To ensure long-term success, you must adopt advanced strategies that go beyond basic adjustments.
Utilizing Machine Learning and Artificial Intelligence (AI)
Advanced control systems may incorporate AI that:
- Analyzes Historical Data: To predict adjustments needed in real time.
- Optimizes Parameters Automatically: Based on continuous performance metrics.
- Reduces Human Intervention: Allowing operators to focus on more complex issues.
Integrating Cloud-Based Monitoring Systems
Cloud solutions offer:
- Remote Diagnostics: Monitor multiple machines across facilities.
- Continuous Data Analysis: For trend identification and proactive adjustments.
- Centralized Reporting: Facilitating decision-making based on aggregated data.
Customizing SOPs and Training Programs
Tailor your maintenance and operational procedures based on:
- Feedback from Operators: Incorporate practical insights from daily operations.
- Evolving Technology: Update procedures to integrate technological upgrades.
- Benchmarking Data: Compare performance across multiple production runs to identify best practices.
Implementing a Step-by-Step Adjustment Process
You can adopt a structured process to achieve consistency in tablet weight. Follow these key steps:
Step 1: Pre-Adjustment Data Collection
- Collect Sample Tablets: Measure weight and record deviations.
- Document Machine Settings: Note current feed rate, compression force, and cycle time.
- Analyze Data: Identify trends and variances in tablet weight.
Step 2: Making Incremental Adjustments
- Adjust One Parameter at a Time: Begin with compression force.
- Monitor Output: After each adjustment, run a test batch and record results.
- Keep Records: Use a log to track changes and outcomes, ensuring you can replicate successful adjustments.
Step 3: Verification and Quality Checks
- Conduct Physical and Digital Inspections: Confirm that adjustments yield the desired tablet weight.
- Implement In-Line Quality Control: Use sensors to continuously check weight consistency during production.
- Adjust as Needed: Refine settings until the target tablet weight is consistently met.
Troubleshooting Tips and Best Practices
Despite careful adjustments, you may still encounter challenges. Use the following troubleshooting tips to address issues quickly:
Tip 1: Monitor Environmental Conditions
- Control Ambient Temperature: Use HVAC systems to maintain stable conditions.
- Manage Humidity: Ensure the production area is neither too dry nor too humid, as both can affect tablet weight.
Tip 2: Routine Equipment Calibration
- Schedule Regular Calibration: Prevents deviation over time.
- Use Digital Tools: Employ the machine’s in-built diagnostic systems.
- Document Changes: Maintain logs for continuous improvement.
Tip 3: Operator Communication and Feedback
- Implement Daily Briefings: Encourage operators to report anomalies.
- Facilitate Knowledge Sharing: Use in-house training sessions to communicate tips.
- Establish a Rapid Response Team: For immediate troubleshooting if weight discrepancies occur.
The Role of Preventative Maintenance
To avoid repeated adjustments and unforeseen downtime, you must adopt robust preventative maintenance strategies.
Daily, Weekly, and Monthly Checklists
- Daily: Visual inspections and pre-run checks.
- Weekly: Cleaning and minor recalibrations.
- Monthly: Comprehensive service, including software updates and mechanical alignment checks.
- Quarterly: Professional audits and deep maintenance sessions.
Long-Term Cost Benefits
Preventive maintenance:
- Reduces Downtime: Minimizes losses due to machine failure.
- Extends Equipment Life: Protects your investment in technology.
- Ensures Consistency: Maintains quality and regulatory compliance.
Operator Training and In-House Expertise Development
Your team’s expertise is invaluable for maintaining operational efficiency. Investing in training programs ensures that operators are well-equipped to handle adjustments and troubleshoot issues effectively.
Training Programs
- Hands-On Workshops: Offer practical sessions on using and adjusting your Tablet Press machine.
- Online Tutorials: Provide digital resources that cover advanced features and adjustment techniques.
- Periodic Refresher Courses: Keep your team updated with the latest technological improvements.
Building a Culture of Continuous Improvement
Encourage operators to:
- Suggest Process Enhancements: Reward initiatives that lead to improved tablet weight consistency.
- Collaborate Actively: Share experiences and insights to refine SOPs continually.
Innovations in Tablet Weight Adjustment Technology
As technology evolves, so do the methods available for adjusting tablet weight. Emerging innovations offer opportunities for even greater precision.
Smart Tablet Press Machines
- Integrated Sensors and AI: Machines are now capable of auto-correcting weight variances.
- Predictive Analytics: Data-driven insights help forecast necessary adjustments.
- Seamless Integration: Smart systems connect with cloud platforms for real-time monitoring and diagnostics.
Digital Twin Technology
- Virtual Simulation: Use digital replicas of your machine to simulate adjustments and predict outcomes.
- Risk-Free Testing: Experiment with settings in a virtual environment before applying changes on the floor.
- Optimization Insights: Gain feedback on potential improvements without disrupting production.
Comparative Summary of Adjustment Methods
To help you navigate the complexities of tablet weight adjustment, refer to the table below:
Adjustment Method |
Target Parameter |
Key Benefits |
Application |
Compression Force Adjustment |
Tablet density and weight |
Increases tablet weight consistency |
Adjust using digital controls or manual dials |
Feed Rate Modification |
Material input rate |
Ensures uniform material supply |
Fine-tune based on sensor feedback |
Cycle Time Adjustment |
Tablet compression duration |
Affects density and tablet hardness |
Modify cycle times to optimize weight |
Die and Punch Alignment |
Tablet shape and uniformity |
Reduces misalignment errors |
Regular mechanical calibration |
Material Property Modification |
Moisture, granularity, and flow properties |
Ensures optimal powder behavior |
Adjust environmental controls and material formulation |
Digital System Optimization |
Overall process automation |
Provides real-time adjustments |
Utilize IoT and cloud-based monitoring systems |
This table concisely summarizes the primary methods available for adjusting tablet weight during operation and helps you choose the most appropriate approach based on your production needs.
Developing an Action Plan for Optimal Tablet Weight
You must integrate all these strategies into a coherent action plan that suits your facility’s specific requirements.
Step-by-Step Action Plan
-
Data Collection and Analysis:
- Gather baseline metrics for tablet weight and process parameters.
- Analyze environmental conditions, machine settings, and material properties.
-
Initial Adjustments:
- Start with the most critical parameter (e.g., compression force).
- Implement incremental changes and record the impact.
-
Performance Testing:
- Conduct test runs and sample measurements.
- Compare the results with baseline data.
-
Review and Feedback:
- Hold a review meeting with operators and technicians.
- Discuss any anomalies and refine adjustments.
-
Implementation of Digital Controls:
- Integrate sensor data and digital controls for auto-adjustments.
- Set up alerts for deviations from target tablet weight.
-
Ongoing Monitoring:
- Establish continuous monitoring through IoT devices and cloud analytics.
- Schedule regular recalibration and maintenance sessions.
-
Documentation and SOP Updates:
- Document every adjustment step and outcome.
- Regularly update SOPs based on new data and feedback.
Following this plan ensures that your adjustments are both methodical and reproducible.
Future Trends and Innovations in Tablet Weight Adjustment
You should stay informed about the latest advancements that will further enhance tablet weight adjustment. Emerging trends that impact this area include:
- Enhanced AI Integration: More advanced predictive models will offer real-time decision support.
- Robotic Automation: Increased automation in adjusting parameters will reduce the need for manual intervention.
- Continuous Improvement Platforms: Integrating all data sources into one platform allows for holistic process optimization.
By embracing these trends, you ensure your production process remains competitive and future-proof.
Conclusion
In summary, you now have a detailed guide on how to adjust the tablet weight during the operation of the tablet press. By implementing systematic adjustments, preventive maintenance, and leveraging digital tools with both Tablet Press machine and Rotary Tablet Press machine systems, you can ensure optimal consistency and compliance. For tailored advice or further technical details, leave a comment or contact us directly. Your proactive adjustments today secure superior tablet quality tomorrow.