In the production of pharmaceuticals and health products, the precision and consistency of capsule filling are key aspects of quality control. Ensuring that each capsule is filled accurately and uniformly is not only a necessary condition to meet regulatory requirements but also the foundation for improving product quality and customer satisfaction. This article will explore solutions to common problems in the capsule filling process, and provide a detailed introduction to the relevant production processes, equipment maintenance, and quality control procedures, with references to pharmaceutical industry standards and regulations to ensure the accuracy and reliability of the content.
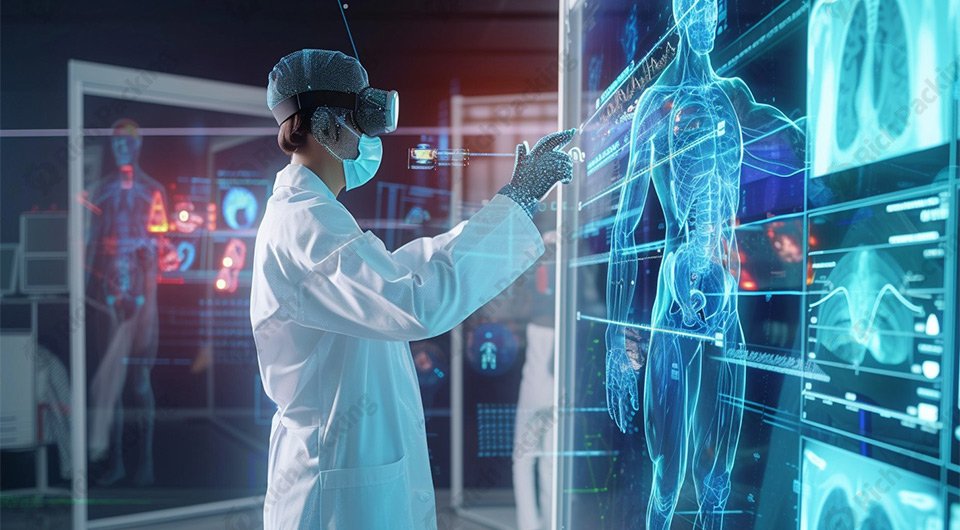
I. Capsule Filling Production Process
Process Flow
Raw Material Preparation: Pre-treat the drug powder or granules, including steps such as drying, crushing, and sieving, to ensure the fluidity and uniformity of the raw materials.
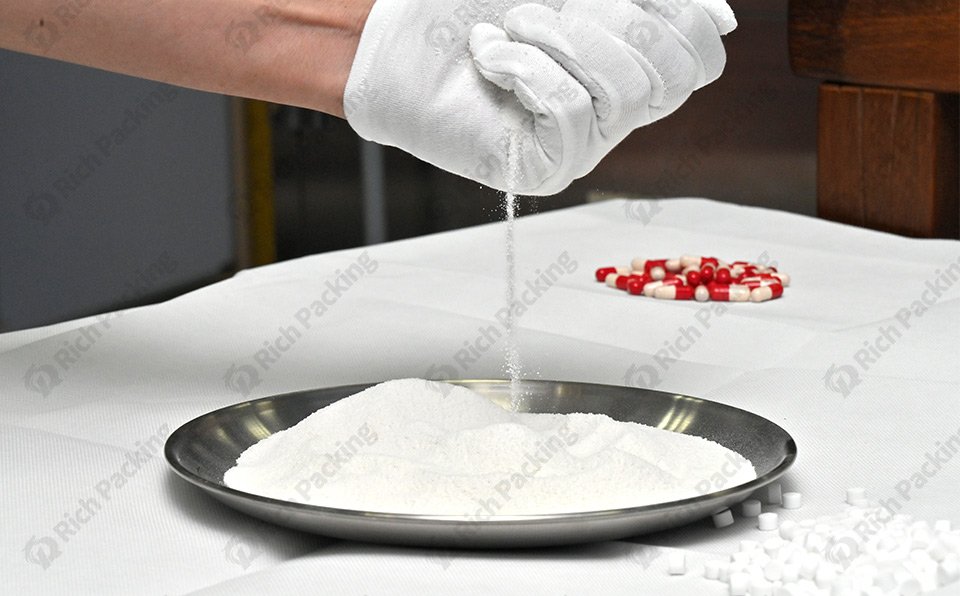
Capsule Shell Treatment: Capsule shells are usually made of gelatin or HPMC and must undergo quality inspection to ensure they are free from damage and contamination.
Filling Process:
- (1) Capsule Arrangement: Arrange the capsules according to the direction of the upper and lower parts and then place them into the capsule tray or mold.
- (2) Capsule Shell Separation: Separate the upper and lower parts of the capsule shell through the capsule separation mechanism.
- (3) Filling Medicine: Use a filling machine to fill the medicine into the lower half of the capsule shell. The filling amount is quantified according to the formula and controlled by the filling equipment, ensuring the medicine dosage is accurate and uniform.
- (4) Sealing the Capsule: Align and seal the upper and lower parts of the capsule shell.
Post-treatment:
The filled capsules need to be polished and screened to remove surface dust and defective products.
Packaging and Storage:
All capsules that pass quality inspection will be packaged in a standardized manner in a pollution-free environment and stored in a warehouse with well-controlled temperature and humidity to maintain their efficacy and quality.
II. Equipment Selection
In the process of capsule filling, selecting the right equipment is key to ensuring the precision and consistency of the filling. High-quality equipment not only improves production efficiency but also reduces problems that may arise during the production process. The following is a detailed introduction and selection recommendation for various types of equipment in the capsule filling process.
The capsule filling machine is the core equipment in the capsule production process, mainly responsible for accurately filling the drug powder or granules into the capsule shell. According to the level of automation, capsule filling machines can be divided into semi-automatic and fully automatic capsule filling machines. Different types of capsule filling machines have their own advantages and applicable scenarios. The following is a detailed introduction and selection recommendation for these two types of filling machines.
1.Semi-automatic Capsule Filling Machine
Semi-automatic capsule filling machines require some manual intervention during the operation process, usually including the following steps:
- a. Capsule Arrangement: Automatically arrange the hard capsules and place them into the mold.
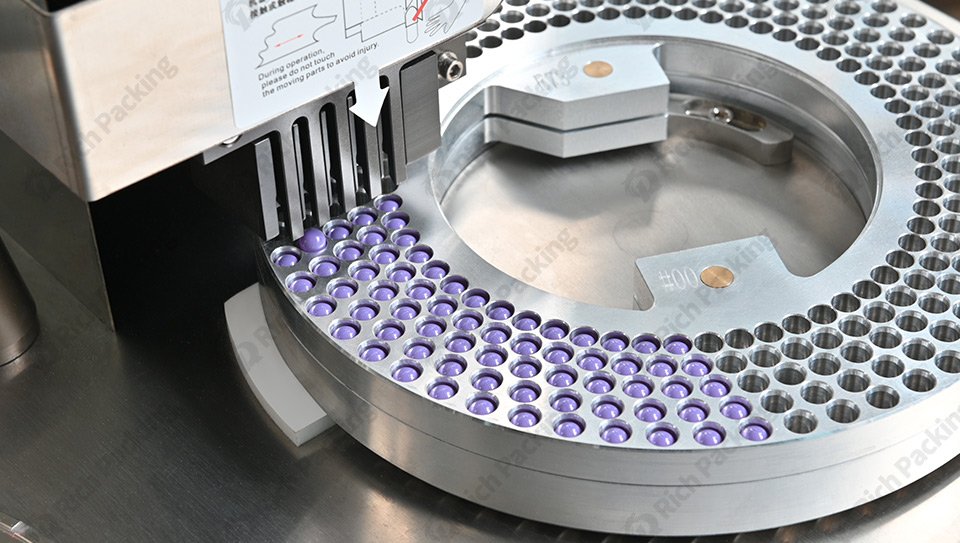
- b. Capsule Shell Separation: The operator rotates the capsule tray on the device to automatically separate the upper and lower shells.
- c. Filling Medicine: The medicine is automatically filled into the lower half of the capsule shell by the machine.
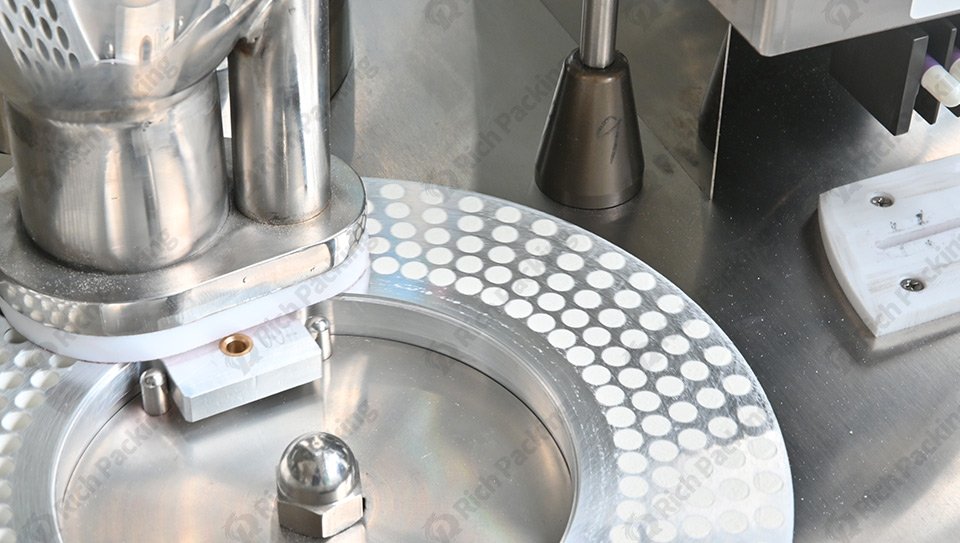
- d. Sealing the Capsule: The operator manually places the capsule tray filled with medicine onto the capsule sealing station, where the machine automatically seals the upper half of the capsule shell to the lower half.
Features of the semi-automatic capsule filling machine:
- High flexibility: Suitable for small batch, multi-variety production, flexible operation, and easy adjustment.
- Lower cost: The equipment price is relatively low, suitable for small and medium-sized enterprises or R&D departments.
- Simple operation: The equipment structure is simple, and operation and maintenance are relatively easy.
Applicable scenarios:
Semi-automatic capsule filling machines are suitable for small and medium-sized enterprises, small batch production, product development, and other scenarios. It is particularly suitable for production lines that require frequent changes in production varieties, such as contract manufacturing organizations (CMOs) and scientific research laboratories.
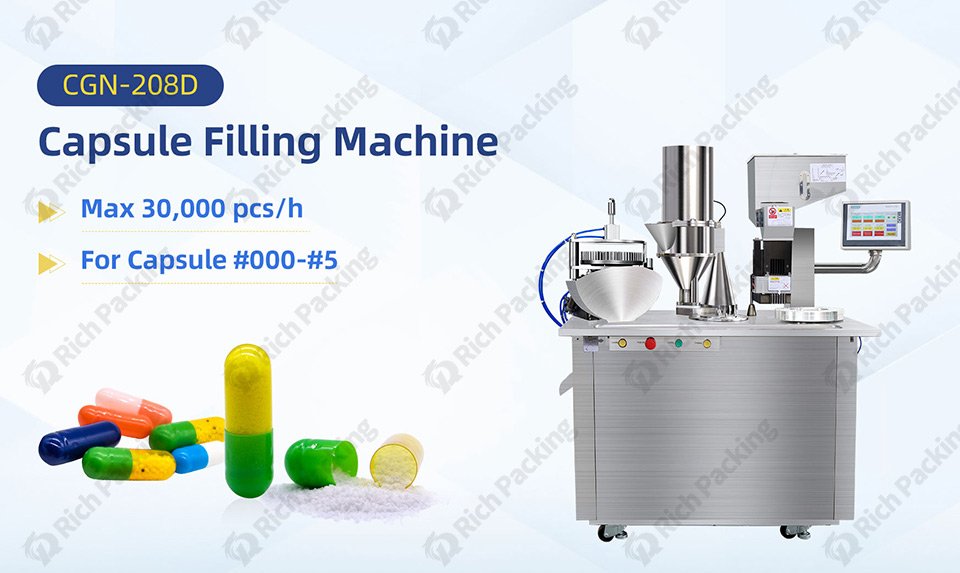
2.Fully Automatic Capsule Filling Machine
Fully automatic capsule filling machines achieve full automation of the capsule filling process, including the following steps:
- a. Sorting: The equipment automatically places the capsules into the mold according to the upper and lower positions of the capsule heads and bodies.
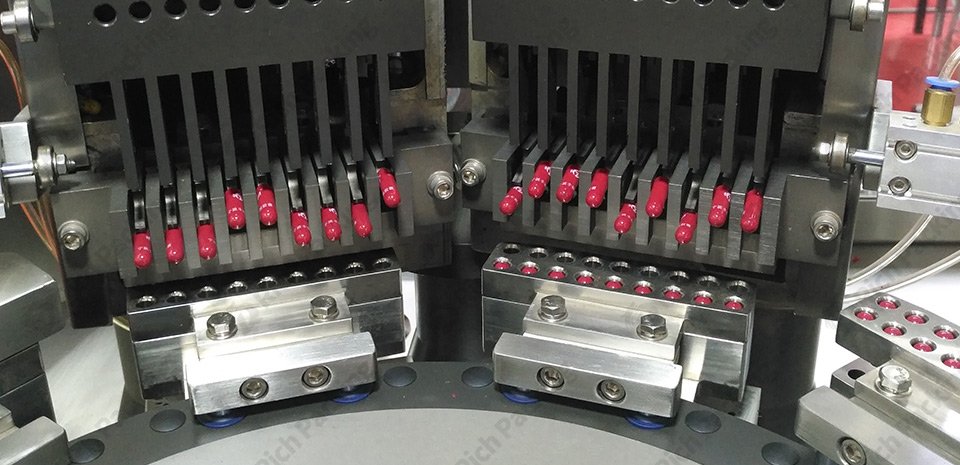
- b. Capsule Shell Separation: The equipment automatically separates the upper and lower parts of the capsule shell through the mold machine's vacuum negative pressure suction.
- c. Filling Medicine: The medicine is precisely filled into the lower half of the capsule shell through an automated system powder metering disc.
- d. Reject Detection: Fully automatic capsule filling machines have a reject function that can automatically remove improperly separated capsule shells.
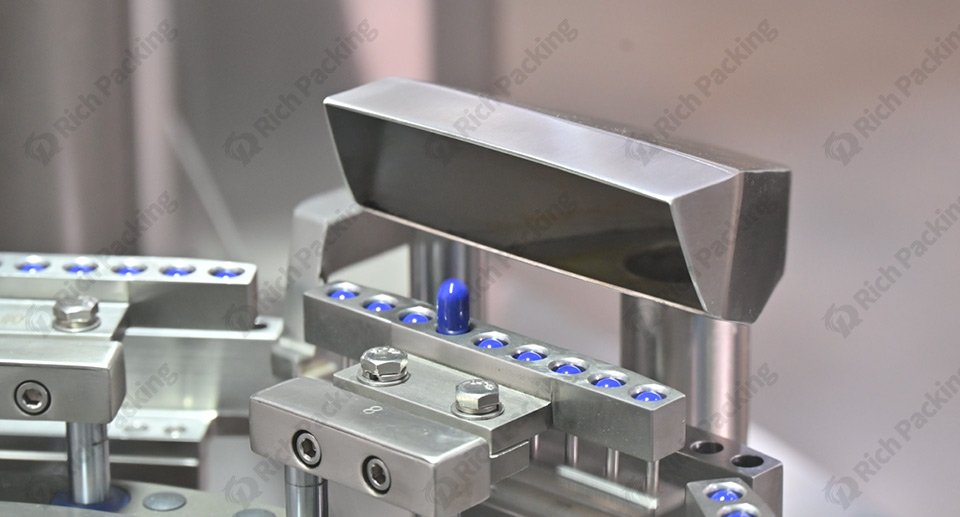
- e. Sealing the Capsule: The equipment automatically seals and locks the upper and lower parts of the capsule shell. f. Polishing and Inspection: Some fully automatic equipment also integrates polishing and weight inspection functions to further improve production efficiency and quality control.
High efficiency: Fully automatic operation greatly improves production efficiency, suitable for mass production.
High precision: Advanced control systems ensure filling precision and consistency, with accurate dosage for each capsule.
Intelligent control automation technology: Intelligent control technology is used to monitor and adjust production parameters in real-time, achieving a stable production process.
Applicable scenarios:
Fully automatic capsule filling machines are suitable for large pharmaceutical companies, mass production lines, highly automated production environments, and other scenarios. It is particularly suitable for production lines with high requirements for output and efficiency, such as companies focused on large-scale commercial production.
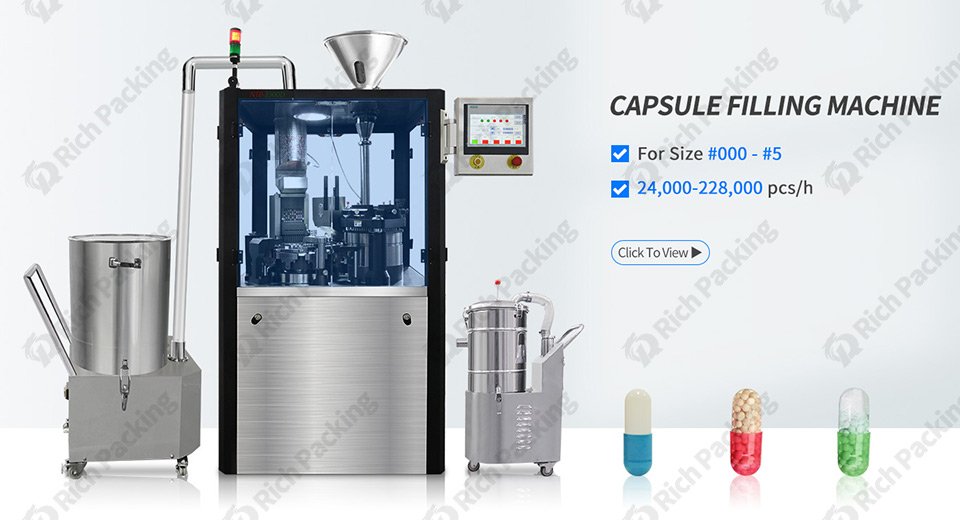
Weighing Equipment
Weighing equipment plays a crucial role in quality control during the capsule production process, ensuring that the filling amount of each capsule meets the predetermined standard, thus ensuring product quality consistency and safety.
Functions and Features
Real-time monitoring: Real-time measurement of the weight of each capsule through high-precision sensors.
Automatic rejection: The equipment automatically rejects capsules that are overweight or underweight.
Data recording and analysis: Records the weight data of each batch of capsules for subsequent analysis and quality traceability.
Other auxiliary equipment: Such as polishing machines, screening machines, etc., to ensure that the appearance and quality of the capsules meet the standards.
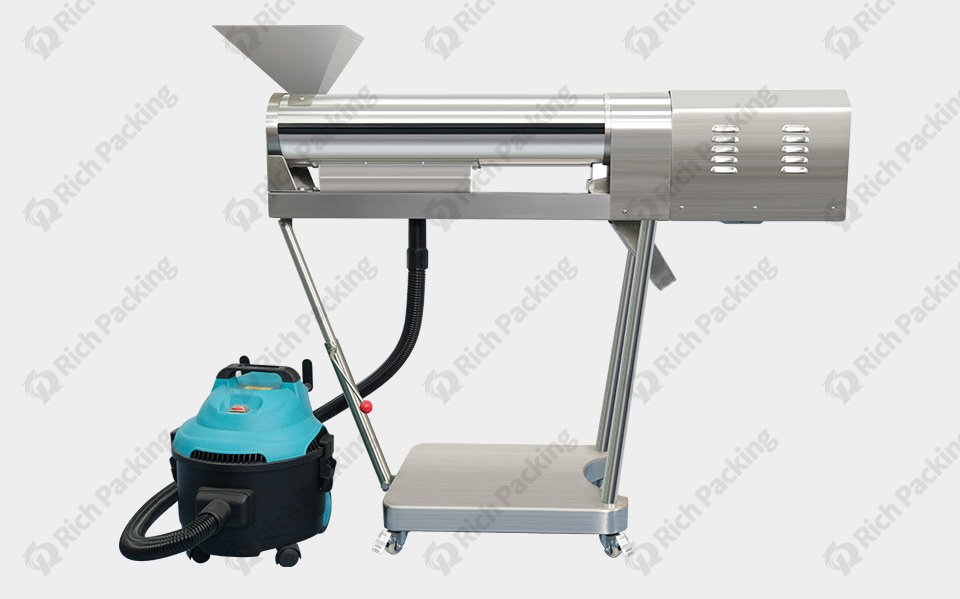
(Capsule polishing machine)
III.Common Problems and Solutions
Filling Inconsistency
Problem Description: The filling amount of the capsules is inconsistent, leading to dosage errors. This problem may be caused by poor powder fluidity, improper calibration of filling equipment, or unstable production environment.
Solutions:
1.Optimize powder characteristics:
- a. Improve powder fluidity: Improve the fluidity of the powder through processes such as crushing, sieving, and drying. A suitable amount of flow aids such as talcum powder or silica gel can be added.
- b. Uniform mixing: Ensure uniform mixing of raw materials and excipients, using efficient mixing equipment such as V-type mixers or three-dimensional mixers.
2.Adjust filling equipment:
- a. Equipment calibration: Regularly calibrate filling equipment to ensure the accuracy of each filling head. Use standard weights for weight calibration to ensure the equipment works accurately within the set dosage range.
- b. Optimize filling head design: Use precision-machined filling heads to reduce powder adhesion and blockage during the filling process.
3.Environmental control:
- a. Temperature and humidity control: Maintain a stable production environment, including temperature and humidity. Generally, it is recommended to control the temperature between 20-25°C and humidity between 40-60% RH.
- b. Anti-static measures: Install anti-static equipment in the production environment to reduce poor fluidity caused by electrostatic adsorption of powder.
Capsule Shell Rupture
Problem Description: The capsule shell ruptures during the filling or sealing process, affecting the product's pass rate. This may be due to substandard capsule shell quality, excessive equipment pressure, or unsuitable environmental humidity.
Solutions:
Choose high-quality capsule shells:
- a. Raw material selection: Choose high-quality capsule shell suppliers that meet pharmaceutical industry standards to ensure the toughness and strength of the capsule shells.
- b. Quality inspection: Conduct strict quality inspections on incoming capsule shells, including hardness testing and thickness measurement.
Equipment optimization:
- a. Separation equipment adjustment: Check and adjust the capsule shell separation equipment to ensure minimal stress on the capsule shells during separation.
- b. Sealing equipment adjustment: Adjust the pressure and temperature parameters of the sealing equipment to ensure that the capsule shells are not overly stressed during the sealing process.
Environmental humidity control:
- a. Humidity regulation: Maintain suitable humidity in the production environment, generally recommended to be controlled between 40-60% RH. Low humidity can cause the capsule shells to become brittle, while high humidity can soften them.
- b. Storage condition optimization: Capsule shells should be stored under suitable temperature and humidity conditions to avoid environmental changes.
Powder Leakage
Problem Description: Drug powder leakage during the filling process leads to inaccurate dosages and equipment contamination. Leakage may be caused by poor equipment sealing, static electricity issues, or poor powder fluidity.
Solutions:
Sealing check:
- a. Equipment sealing check: Regularly check the sealing of the filling equipment to ensure good sealing conditions at all connection points and filling heads.
- b. Replace sealing parts: Timely replacement of worn sealing rings, gaskets, etc., to ensure the sealing performance of the equipment.
Cleaning and maintenance:
- a. Regular cleaning: Strengthen the cleaning and maintenance of the equipment, especially filling heads, guide rails, etc., to prevent the accumulation and leakage of drug powder.
- b. Cleaning records: Establish equipment cleaning records to ensure detailed records after each cleaning for traceability and inspection.
Anti-static measures:
- a. Install anti-static equipment: Install anti-static equipment in the production environment, such as static eliminators, ion wind sticks, etc., to reduce powder dispersion during the filling process.
- b. Personnel anti-static equipment: Operators should wear anti-static clothing and shoes, use anti-static wristbands to reduce the generation and accumulation of static electricity.
Powder fluidity improvement:
- a. Add flow aids: Add a suitable amount of flow aids to the powder to improve its fluidity and filling efficiency.
- b. Adjust process parameters: Adjust the parameters of the filling equipment according to the characteristics of the powder, such as filling speed, vibration frequency, etc., to optimize the filling process.
-
Inconsistent Capsule Weights
Problem Description: Inconsistent capsule weights can lead to dosage errors, affecting the efficacy and safety of the medication. This may be caused by inaccurate filling equipment, uneven raw materials, or improper control of the production process.
Solutions:
Equipment calibration and maintenance:
- a. Regular calibration: Regularly calibrate the filling equipment to ensure the dosage consistency of each filling head. Use standard weights for weight calibration.
- b. Equipment maintenance: Regularly inspect worn parts of the equipment and replace them promptly to ensure stable operation.
Raw material uniformity:
- a. Uniform mixing: Ensure the uniform mixing of drug powder and excipients, using efficient mixing equipment such as V-type mixers or three-dimensional mixers.
- b. Particle size control: Control the particle size of the powder to ensure uniform particle size and reduce dosage fluctuations during the filling process.
Production process control:
- a. Process parameter monitoring: Strictly control the process parameters of the filling machine, such as filling speed and pressure, to ensure the stability of the production process.
- b. Real-time monitoring: Install a real-time monitoring system to promptly detect and handle abnormalities in production and reduce the problem of inconsistent weights.
-
Capsule Surface Contamination
Problem Description: Capsule surface contamination affects the appearance and quality of the product. This may be caused by an unclean production environment, inadequate equipment cleaning, or improper personnel operation.
Solutions:
Environmental cleaning:
- a. Clean production environment: Maintain cleanliness in the production workshop, regularly clean and disinfect to reduce dust and microorganisms in the air.
- b. Air purification equipment: Install air purification equipment, such as high-efficiency particulate air (HEPA) filters, to ensure the cleanliness of the production environment.
Equipment cleaning:
- a. Cleaning standards: Develop detailed equipment cleaning standards to ensure thorough cleaning of the equipment after each production.
- b. Regular inspection: Regularly inspect the cleaning condition of the equipment to prevent drug residue and cross-contamination.
Operational standards:
- a. Personnel training: Train operators to improve their operational skills and hygiene awareness to ensure standardized operations.
- b. Wear protective equipment: Operators must wear complete personal protective equipment, such as gloves, protective masks, and cleanroom-specific clothing, to reduce direct contact with capsules.
-
Equipment Maintenance and Optimization
Regular Maintenance
- Clean equipment: Thoroughly clean the filling equipment after each production shift to prevent drug residue and cross-contamination.
- Check wear parts: Regularly inspect the consumable parts of the equipment, such as seals, belts, etc., and replace them promptly to ensure normal operation.
- Calibrate instruments: Regularly calibrate weighing sensors, photoelectric sensors, etc., to ensure measurement accuracy.
-
Equipment Upgrade
- Introduce automation technology: Improve production line efficiency and stability through automated equipment and system integration.
- Real-time monitoring system: Install a real-time monitoring system to promptly detect and handle abnormalities in production.
- Intelligent control: Use intelligent control technology to optimize filling process parameters and improve product consistency.
Quality Control Process
Raw Material Control
- Raw material inspection: Strictly inspect raw materials entering production to ensure they meet quality standards.
- Batch management: Establish a complete batch management system to track the source and usage of each batch of raw materials.
Production Process Control
- Online inspection: Real-time monitoring of each link of capsule filling through online inspection equipment to ensure product quality.
- Process parameter monitoring: Strictly control the process parameters of the filling machine, such as filling speed and pressure, to ensure a stable production environment.
- Personnel training: Regularly train operators to improve their operational skills and quality awareness.
Finished Product Inspection
- Random sampling: Randomly sample finished products at a certain ratio to test their filling amount, appearance, sealing conditions, etc.
- Physical and chemical index testing: Test the dissolution, content uniformity, and other physical and chemical indices of the capsules to ensure they meet pharmacopoeia standards.
Pharmaceutical Industry Standards and Regulations
GMP (Good Manufacturing Practice)
GMP stipulates the basic principles and standards that should be in the pharmaceutical production process, including factory facilities, equipment management, raw material control, production process management, quality control, etc. For specific content, refer to the "Good Manufacturing Practice for Pharmaceutical Production" (GMP).
ISO 9001 (Quality Management System)
The ISO 9001 standard emphasizes continuous improvement of product quality by establishing a systematic quality management system to meet customer needs and legal and regulatory requirements. It is applicable to various industries, including pharmaceutical production.
ICH Q7 (GMP Guide for Active Pharmaceutical Ingredients)
ICH Q7 provides detailed guidance for the production of active pharmaceutical ingredients, including requirements for quality management, personnel, equipment, raw materials, production, packaging, labeling, and documentation, to ensure the quality and safety of APIs.
Conclusion
Ensuring the precision and consistency of capsule filling is a core task in the quality control of pharmaceutical production. By optimizing production processes, strengthening equipment maintenance, strictly controlling quality control procedures, and adhering to relevant industry standards and regulations, the precision and consistency of capsule filling can be effectively improved to ensure product quality meets regulatory requirements and customer needs. It is hoped that the discussions and suggestions in this article can provide a useful reference for pharmaceutical manufacturing enterprises and promote the improvement of quality management standards in the industry.